在竞争激烈的工业制造领域,无锡百安特凭借多年的技术沉淀与市场深耕,始终在行业内占据重要地位。然而,随着市场需求的不断升级,传统生产工艺在效率、精度及质量稳定性上的短板逐渐凸显。尤其是在关键的焊接与加工环节,效率瓶颈与质量波动,成为了企业进一步发展的阻碍。常州海宝带来的 P+T 等离子焊氩弧焊设备、半圆管自动焊机与封头开孔机器人,为无锡百安特注入了全新活力,一场引领行业变革的智造升级由此展开。
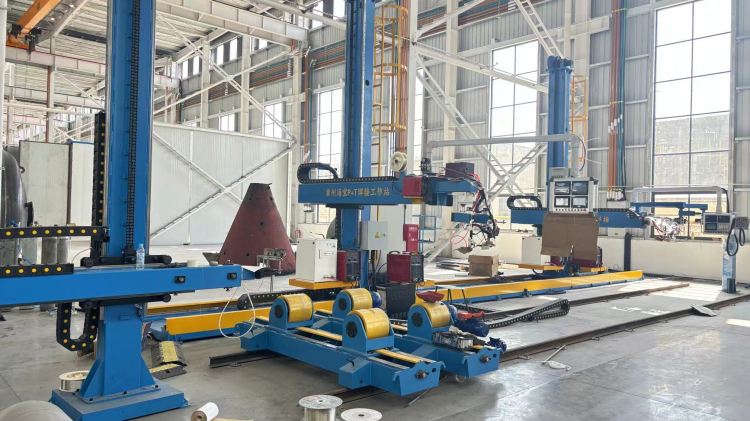
在金属焊接工艺中,12mm 厚度板材的焊接一直是行业难题。传统焊接不仅需经过繁杂的打坡口工序,耗费大量人力与时间,且焊接质量难以保证,气孔、夹渣等缺陷频发,导致拍片探伤合格率长期处于较低水平。此前,无锡百安特在处理此类板材焊接时,同样面临效率低下、废品率高的困境,这严重影响了生产进度与产品口碑。
常州海宝 P+T 等离子焊氩弧焊设备打破了这一困局。该设备创新融合等离子焊与氩弧焊的优势,实现焊接技术的重大突破。等离子焊凭借能量高度集中、电弧温度极高的特性,可瞬间穿透 12mm 厚度板材,形成均匀稳定的熔池,实现单面焊双面成型,且无需打坡口,直接精简前期加工环节,大幅缩短生产周期。
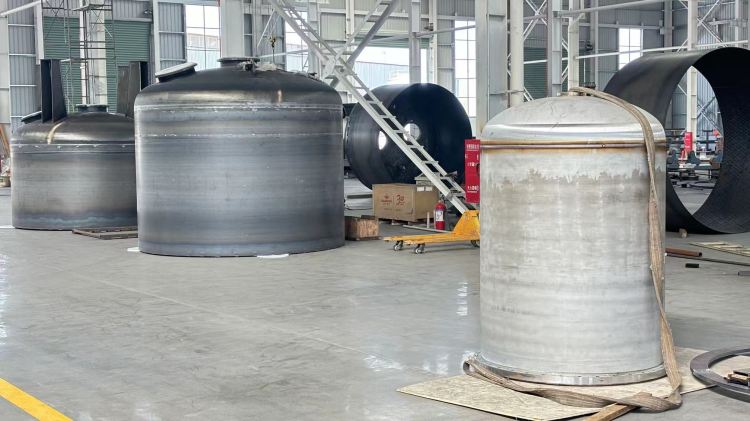
氩弧焊技术则为焊接质量提供坚实保障。等离子焊完成熔接后,氩弧焊以稳定电弧与高纯度氩气,在焊缝周围构建严密保护层,隔绝空气中杂质,有效避免焊缝氧化、气孔等问题。两者协同作用,使焊接后的焊缝外观平整光滑,内部结构致密均匀。
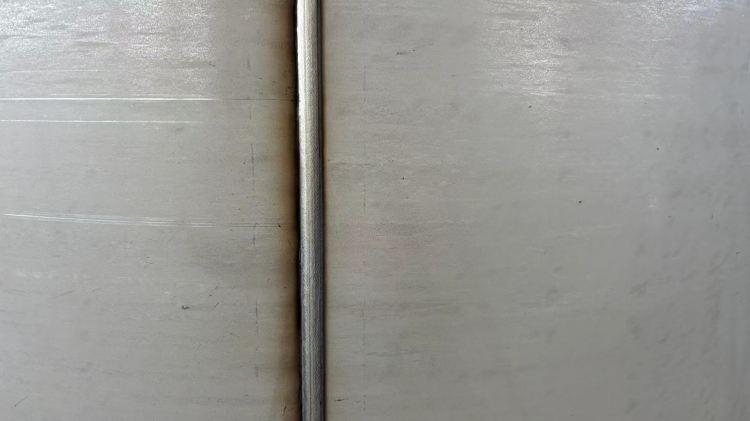
引入该设备后,无锡百安特的生产质量实现飞跃。经专业检测,采用 P+T 等离子焊氩弧焊设备焊接的 12mm 厚度板材,拍片探伤合格率从以往的 70% 左右飙升至 95% 以上。这不仅标志着产品质量达到行业领先水平,更让企业在高端订单承接上拥有强大竞争力。
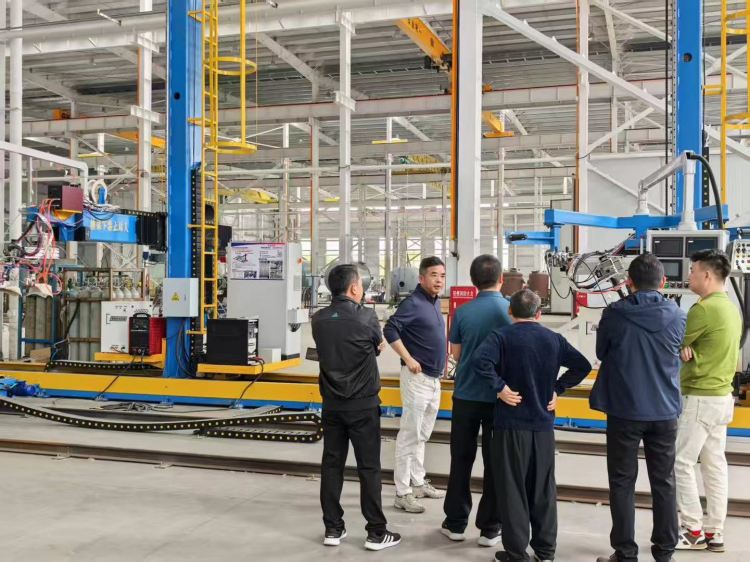
半圆管焊接是无锡百安特产品生产的关键环节,其质量直接影响设备整体性能与使用寿命。以往采用人工氩弧焊,不仅对焊工技术要求极高,且半圆管结构复杂,焊接时需频繁调整焊枪角度与位置,工作强度大、效率低。同时,人工操作难以保证焊缝一致性,焊接质量波动大,返工率居高不下。
常州海宝半圆管自动焊机彻底改变了这一现状。设备配备高精度伺服驱动系统与智能控制系统,可精准控制焊枪运动轨迹与焊接参数。焊接过程中,系统能依据半圆管曲率、管径等参数,自动调节焊接速度、电流、电压,确保每道焊缝达到最佳效果。
其先进的激光视觉传感器赋予设备独特的跟踪与纠偏功能。传感器实时监测焊缝位置,一旦出现偏差,系统立即调整焊枪,保证焊缝始终处于最佳状态。高度自动化的焊接方式,使生产效率大幅提升。实际数据显示,使用半圆管自动焊机后,无锡百安特的半圆管焊接效率较人工焊接提高近 3 倍,原本数天的焊接任务,如今一天内即可高质量完成。
自动焊机的稳定输出,显著改善焊接质量。焊缝均匀性、强度与密封性远超人工焊接,有效降低设备泄漏、腐蚀风险,为客户提供更可靠的产品。
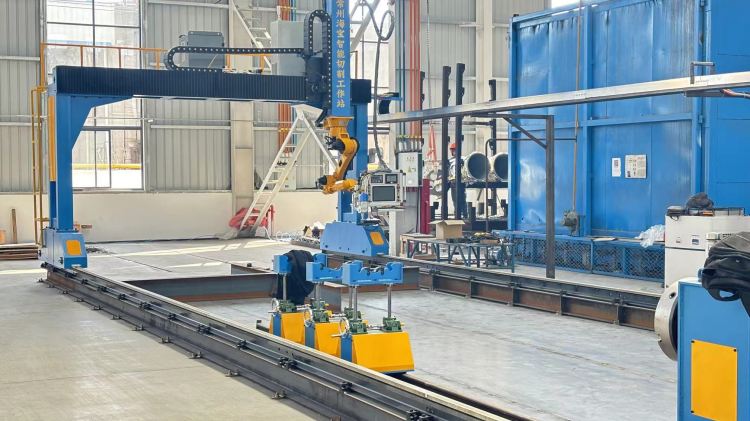
封头作为无锡百安特产品的核心部件,其开孔精度直接影响设备密封性与整体性能。过去,封头开孔依赖人工操作,工人需先划线定位,再用机床开孔。这一过程耗时耗力,且人工误差导致开孔尺寸与位置精度难以保证,常出现偏差,造成材料与时间的双重浪费。
常州海宝封头开孔机器人为无锡百安特带来全新解决方案。机器人搭载先进视觉识别系统与高精度数控系统。视觉识别系统通过高清摄像头快速扫描、定位封头,精准识别尺寸、形状与预设开孔位置;数控系统则依据数据,控制机械臂带动高精度刀具作业。
开孔过程中,机器人机械臂运动灵活精准,重复定位精度达 ±0.02mm,可满足各种复杂形状与尺寸的开孔需求。与传统人工开孔相比,效率提升高达 5 倍以上,以往数小时的工作,如今十几分钟即可高质量完成。
机器人的高精度作业大幅提升开孔质量。开孔尺寸精确、边缘光滑平整,显著提高封头与其他部件的组装匹配度,减少后续打磨、修整工序,进一步缩短生产周期。同时,自动化操作降低工人劳动强度,提升生产安全性。
无锡百安特与常州海宝的深度合作,借助 P+T 等离子焊氩弧焊设备、半圆管自动焊机、封头开孔机器人三件先进设备,实现生产工艺的全面升级。从焊接质量到加工效率,从产品精度到产能提升,均取得令人瞩目的成果。这场技术革新让无锡百安特在市场竞争中脱颖而出,更为整个行业发展提供新思路与方向。未来,随着双方合作持续深入,必将为工业制造领域带来更多创新突破,书写中国制造业的辉煌新篇章。
查看所有评论(总共0条)评论列表